The History Of The Consett Iron Company
Chapter One
The Iron Works First Twenty Four years In Operation 1841 to 1865
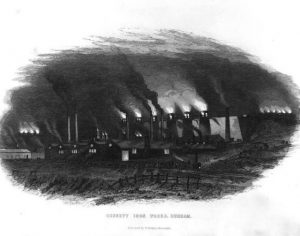
The history of the beginning of “Consett Iron Company”. The Company was created In 1840 by Mr. Johnathon Richardson under the name of the “Derwent Iron Company”. In 1857 the Derwent Iron Company fell on hard times, as a result, the Derwent and Consett Iron Company was formed to take over its assets. Not long after, Derwent and Consett Iron Company was then put up for sale and taken over by the “Consett Iron Company Ltd.” in 1864. The Consett Iron Company Ltd was situated 14 miles south-west of Newcastle, to which there was communication by the Blaydon and Consett Railway, and 14 miles from the classic region of Durham, to which there was communication by an extension of the same railway by way of Lanchester. The situation was chosen, in the first instance, as being advantageous for a supply of ironstone and coal, as well as limestone. As regards ironstone, this advantage no longer existed. Supplies were now brought in from distant parts, principally from Cleveland and the hematite mines of Cumberland. Notwithstanding this drawback, the Derwent and Consett Iron Company had been remarkably prosperous.
The People In Charge
Mr. John Henderson, M.P. was the chairman of this company. Mr. Thomas Spencer vice-chairman, Mr. David Dale was managing director and Mr. William Jenkins general manager. Employment was given to approximately 3,000 people. The paid-up shares of £7 10s were then quoted as £3 12s 6d Premium. As a result, the works were still being extended, in anticipation of increased trade.
The Detailed Makings of Consett Iron Company
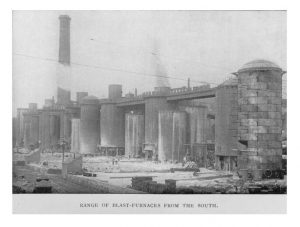
The establishment at Consett consisted of blast-furnaces, forges, rolling-mills workshops, and offices. There were three blast-furnaces in action; two more were in course of erection. The height of those in action was about 55ft.; eight cast-iron columns supported the body of each. Their diameter at the boshes varied from 20 to 22.5 ft. The pig iron in each, average 450 tons per week.
The top of each furnace is closed, on the cup and cone method and the gases are withdrawn for heating the whole of the stoves and boilers without the need of any coal for these purposes. A chimney 250ft. In height and 22ft.inside diameter at the base, decreasing in size towards the top is the medium for withdrawing the gases from the furnaces, and would serve for those which would come into operation afterward.
Stoves
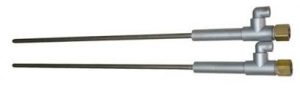
The stoves used at No. 3 furnace were of cast iron of which there were 5. The principle of this stove was a combustion-chamber below. There were 18 double pipes, in six rows, in each stove. The pipes were 8in. diameter, and 17ft.in length. The blast traversed two pipes at once, through 18 lengths before it made its exit at the delivery valve. The blast at no. 4 and 5 furnaces was heated by the Whitwell brick stoves. These had been so frequently explained that it was unnecessary to give any detailed account of them. They seemed, after 18 month’s experience of their working, to be much approved of, as a result, others were intended to be added to the furnaces in the course of their erection.
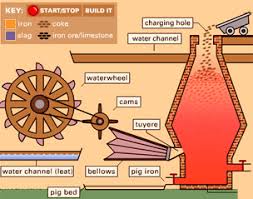
Flues
There were twelve 9in. Flues, and eleven 7in. brick partitions in
each, for the passage up and down of ignited gas, for a period of two hours. The blast is heated by contact with the brickwork in those passages during the next two hours, and so on alternately. The blast was heated from about 1300 degrees at the commencement to 2100 degrees at the end of each alternate period of two hours.
Bricks
The bricks for the construction of these stoves were made at the Consett Company brickworks and were well adapted for the intense heat generated in them by the ignition of the gas. The blast was conveyed to the tuyere pipes of each furnace by a wrought-iron circular main, 2ft. 9in. in diameter. This was lined with 9in. brickwork, hence reducing the size internally to 18in. There were five tuyeres to each furnace, equidistant. A wrought-iron downpipe from each furnace was lined with 3in. brickwork. These conveyed the waste gas into a main underground culvert which extended in a straight line behind the furnaces, from where it was taken at various points to be utilized in the stoves and under the boilers.
Blowing engines
The main blast pipe was 5ft. in diameter, this meant the blast having free communication from all the engines throughout this tube. This blast pipe consisted of, firstly two blowing engines in one house (at one extremity), of equal size and working independently (The beam of each was supported on a cast-iron standard). Secondly, steam cylinders 37in., Thirdly, blowing cylinders 90in., with an 8ft. stroke, going at the rate of 18 strokes per minute. Fourthly, flywheels 2ft. diameter, each worked by a connecting rod between the steam cylinder and center. The result of pressure for the blast was about 3.5lbs.
Two other blowing engines in one house, also working independently, had been in action for a while but only one was now going, at the rate of 20 strokes per minute. The other engine was in course of alteration, the beam of which was placed on cast-iron standards, instead of resting on girders fixed in the sidewalls of the house. The blowing cylinders of these were 81in. in diameter, with an 8ft. stroke. There were six plain cylindrical boilers for these engines, 70ft. in length, 4.5ft. in diameter.
Boilers
There were six plain cylindrical boilers for these engines and were 70ft. in length and 4.5ft. in diameter. The boilers were suspended from five girders, which crossed continuously over the six boilers, having intermediate pillars of support and resting on stone foundations. Each boiler was suspended from the girders by three straps at five points and the pressure of steam was from 40 to 45lbs. These boilers were covered by a wooden shed.
There were eight plain boilers connected to the two engines first described and these were made 35ft. Long 4.5ft. diameter, to avoid the great strain to which the long boilers were subjected too. The 35ft. boilers were suspended from girders in a similar manner to the others and were covered over with brickwork.
Crookhall
The produce of pig iron in those three furnaces and two others at Crookhall was at that time 2000 tons per week. The two new furnaces were designed to be of similar capacity and producing powers to those that were in operation at the Consett Iron Company and to be furnished with the Whitwell brick stoves, and all improvements for economizing labor and reducing the cost of production.
Two blowing engines were intended to be built in line with the others to meet the requirements of those extensions. The ironstone and limestone were tipped from the trucks on elevated ground, 10ft. below the level of the charging-plate of the furnaces; 186 coke ovens were built on the same ground for the supply of coke and these materials were all conveyed by means of an inclined plane and horizontal steam engine to the top of the three furnaces.
The pig iron produced at the Consett Iron Company and Crookhall furnaces were almost entirely manufactured at the forges and mills erected contiguous to the blast-furnaces at the Consett Works; 156 puddling-furnaces were erected. Five steam hammers were at the works operating upon the puddle balls. There were two forge engines and one of these drove three pairs of puddling rolls on each side of it.
There were five rolling-mills; at one of these, rails were manufactured and having the entire requisite appliances in connection with it for sawing, punching, and straightening.
Rolling Mills
The other four mills were exclusively for rolling ship-plates, as a result, the Consett iron was specially adapted to this purpose, for the manufacture of which of various sizes and qualities these mills were constantly in action on weekdays and nights. One of the plate mills was on the reversing principle; the rolls are reversed by a clutch fitting into crabs attached to cogwheels on either side, which wheels revolve in opposite directions. Four powerful shears were erected, 7 to 8ft. wide, for cutting the plates, with a separate engine to each.
The product of the plate-mills was very large; hence, 700 tons per week of ship-plates were turned out of these mills. This, we believe was the largest output of plates at any works in this country and probably the largest in the world. Furthermore, the Consett Iron Company was supplying rails to some of the largest English railways and large quantities were also shipped to Russia and America. The number of rails in weight per week was about 700 tons per week, thus giving a total product of 1400 tons of finished iron per week.
Heating The Boilers
Most of the steam boilers for the forge and mill engines were heated by the waste heat from the puddling and mill furnaces. The boilers were placed horizontally, have double tubes, and two iron chimneys attached. Each boiler was supplied with heat from two adjoining furnaces. A few boilers were heated with small coal.
Furnaces
Seven furnaces at Crookhall, 45ft in height were erected at the same time as those at Consett. However, only two of these at that time were in operation. The manufacture of pig iron was intended to be concentrated at the Consett Iron Company and the working of these furnaces, as a result, discontinued. The four blast-furnaces that had been erected at Bradley, subsequently to those at Crookhall, and of the same type, were at that time being taken down.
Coal Deposits
Mr E. F. Boyd was the President of the Northern Mining Institute and was the consulting mining engineer for the company. The coal was all of the bituminous coking quality and obtained from the lowest seams in the coal measures, from the Busty Bank and other seams. The output of coal was about 12,000 tons per week. That being so, part of the coal was sold for gas purposes; the forges and mills used a large quantity of coal.
There were 560 coke ovens at the Consett Iron Company and at other places, nearly all of which were in operation. The coke was very pure, and above all, containing but a small percentage of sulfur and ash and is well adapted for making high-class pig iron.
Transportation Of Materials
To convey materials about the works and at the different pits, consequently, ten locomotive tank engines were in use. The workshops comprised of smith’s, and joiners, wagon shops, and also roll-turning, fitting, and machine-shops, and together with a large foundry, to meet the requirements of concern so extensive as that which we have briefly described. The fire-brick works of this company were capable of making 60,000 fire-bricks per week.
Consett’s Infrastructure
The Consett Iron Company was not failing to attend to the moral and the social well-being of their workmen. The company built most of the schools, as a result, these are dispersed at convenient distances, and every day not less than 1,500 children were educated in the various schools in and about Consett. They are all self-supporting and subsidized by Government grants, but there was still a great lack of desire on the part of the ironworkers and pitmen to send their children to school, as a result, hundreds were not educated at all.
Religion
The Protestants, Dissenters, and Roman Catholics possess well built, and in many cases, handsome churches and chapels. The latter section formed the bulk of the population. They provided their own school buildings. Two buildings were set apart as reading rooms, and provided, together with lights and fuel, by the company. Numerous papers, books, and periodicals were subscribed for by the younger portion of the workmen. Other means of recreation were also provided in connection with these institutions.
Wages
The wages at the Consett Iron Company were all paid in coin. Subsequently, an advance on wages being paid back in one week or fortnightly settlements. A co-operative store was established and managed by the workmen, the sales of which in 1869 reached £18,009 13s 5d. The company possessed 1,500 workmen’s cottages at various points on their property. A staff, of five surgeons, was also provided. The Iron Works provided the surgery, buildings and the lighting, and also an infirmary for workmen injured in the works or pits. The cost being for paid by the company. The workmen contributed to the whole of the cost of these surgeons.
Copyright M. C. Boyle